Rockets Olympus Team
Sep 2019 - Present
with Stanford Student Space Initiative
Our team competes in the yearly Intercollegiate Rocket Engineering Competition. Each rocket carries a payload of 8.8 pounds and has a target altitude of 30,000 ft. Competing rockets are typically 4 to 8 inches in diameter and 8 to 20 ft. long. Multistage rockets and all chemical propulsion types (solid, liquid, and hybrid) are allowed. Our team uses a solid motor but I was delighted to watch other teams deploy their experimental liquid propulsion, often leading to explosive results.
I am on the recovery sub-team. We use black powder and CO2 canisters to deploy the drogue and main parachutes, triggered when desired altitude is detected by sensors. At apogee +2s, a CO2 canister is punctured and black powder is ignited deploying the first parachute. At 1500 ft +2s, the main parachute is deployed. The canister hubs and payload are made using 3D printing and computer-aided design. I also picked up a lot of EE knowledge--wiring, stripping, crimping, and integrating circuit boards.
My biggest takeaway is that duct tape can fix any problem, no matter how large. (Just kidding.) There is a lot of pressure for us to get our part right, because if the rocket crash lands then the avionics, structures, and systems teams will not be happy having to rebuild their work. In addition, if the parachute deploys too early, we have to walk several miles to track down the rocket. That's why it's important to test our ejection mechanism on the ground. The results of our trials were thoroughly documented. We have to explore every avenue to make sure our design doesn't fail. Failure analysis is key.

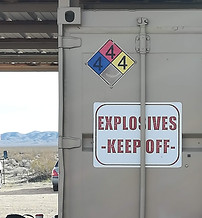

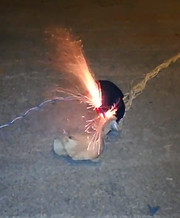
