Stanford Solar Car Project
Sep 2019 - Present
with Stanford Solar Car Team
The Stanford Solar Car Team competes in the World Solar Challenge, where we design and build a vehicle to operate along a 3,000 km outback route in Australia powered only by the energy of the sun. Every system in the car is built from the ground up, including the aerobody, suspension, brakes, and lights.
A lot goes into building a car. We have an electrical, array, battery, and even a racing strategy team. I am on the mechanical team: I have designed parts for the suspension, brakes, headlights/taillights, and wheel shrouds. These parts are drawn up in Fusion 360 and machined in-house or outsourced. Manufacturing these parts requires conducting finite element analysis, machining parts, outlining a bill of materials, and optimizing weight/mass. Communication and interfacing with other subteams is important. For example, when designing the housing for the headlights, I made sure that it would fit with the aerobody and conform to the dimensions of the circuit board specified by the EE team.
An integral project that I worked on over the summer was the suspension--specifically the wheel shrouds. I used Autodesk Fusion 360 to design the wheel shrouds and mounts. I used Fusion's CAM to define the tool passes to create the mold for the wheel shrouds. I used a CNC machine to carve out the mold, following the specifications in CAM. I then performed a carbon fiber layup to make the wheel shrouds. Finally, I finished the part using a belt sander and Dremel. Each of the wheel shrouds posed a unique challenge. The front suspension has an upright that we machined at an angle offset relative to the vertical plane. This meant I had to design a panel mount that started in the plane of the upright but spreads out to the plane parallel to the side of the car. Additionally, I needed to cut out geometry to make sure that the brake caliper did not interfere with the shrouds. The rear suspension, where the motor is mounted, posed another set of challenges. I created a special part that allowed the bolts of the motor hub to screw into the panel mount. This turned out to be a lightweight and space-efficient solution. I believe that the skills I employed in this project allowed for a straightforward manufacturing and assembly process.
Because the car needs to be street-legal, our car design must follow intensely specific guidelines. This means we have to evaluate different specifications and tradeoffs. For instance, our car must be light and efficient but also minimize risk for a rollover crash. This is where napkin math and FEA comes in handy. I use generative design, a feature that allows users to input CAD geometry and load points to cut down on the weight of car parts.


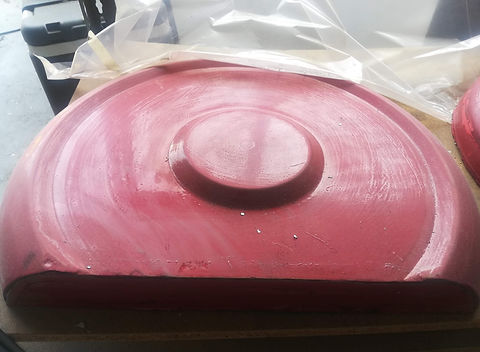
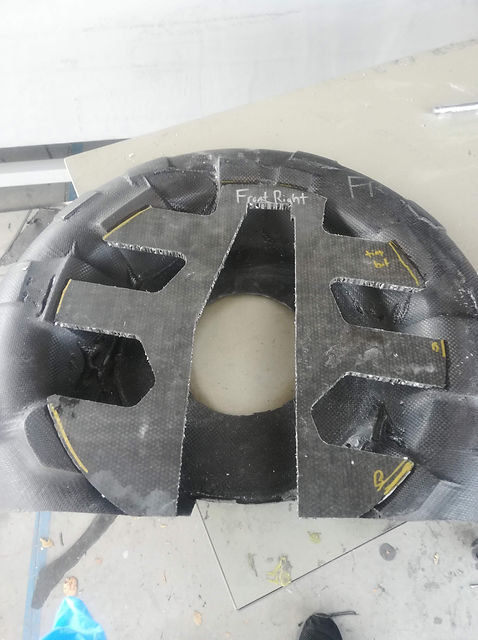
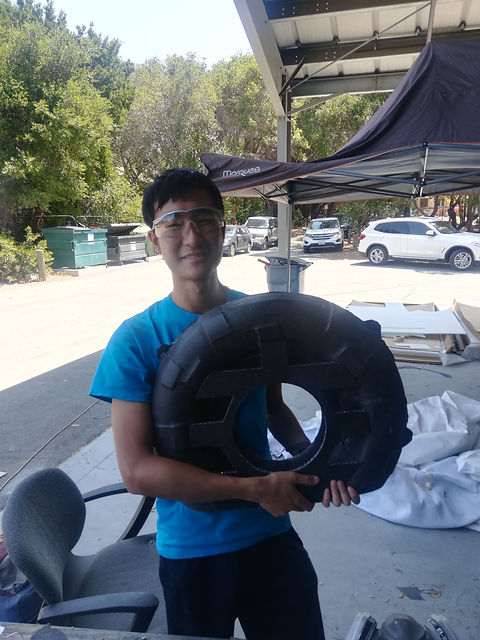







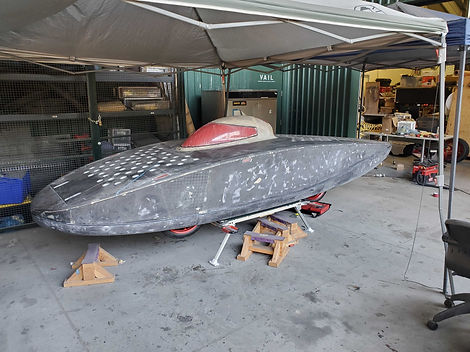

